TPM管理是針對設(shè)備的一種管理工具,它不是為了管理而管理,而是為了設(shè)備在生產(chǎn)過程中發(fā)揮最大的作用,降低設(shè)備的故障率,延緩其使用壽命,降低成本,提高生產(chǎn)量,為企業(yè)創(chuàng)造更高的效益。以下是
TPM管理咨詢公司對TPM提高綜合效率的方案。
TPM設(shè)備管理
TPM管理主要是全員參與維護(hù),是有日本在美國和英國的管理基礎(chǔ)上所總結(jié)得來的一套管理理念,起初,只是簡單的設(shè)備管理維護(hù)工作,降低設(shè)備故障率,提高利用率,而現(xiàn)在,為了滿足更高的需求,TPM還肩負(fù)著提高設(shè)備綜合利用率的使命,具體有以下措施:
1、建立、健全設(shè)備管理檔案及設(shè)備故障履歷
“好腦筋不如爛筆頭”,建立、健全、完善的檔案體系是設(shè)備管理不可缺少的重要環(huán)節(jié)。我們不僅從中了解設(shè)備的使用性能,掌握操作要領(lǐng),而且能夠?qū)嵤┯嗅槍π缘木哂衅涮厣木S護(hù)和檢修方案,充分發(fā)揮潛能。
“知己知彼,方能百戰(zhàn)不殆”。認(rèn)真記錄設(shè)備的性能指標(biāo),詳實記錄各種備件的更換時間、損壞原因以及檢修所需時間,更換周期,建立“維修知識數(shù)據(jù)庫”,提高維修人員技能,縮短維修時間,這些對我們的計劃檢修、備件儲備都具百益而無一害。準(zhǔn)確的管理檔案更是確定大中修周期及內(nèi)容的最可靠的信息來源。檔案管理是指引設(shè)備管理前進(jìn)的航標(biāo)燈,促使設(shè)備管理逐步走向規(guī)范化、現(xiàn)代化、科學(xué)化。
2、建立點檢定修機制,延長設(shè)備的周期使用壽命
點檢定修制是一項重要的設(shè)備管理制度,推行全員參加的以點檢為核心的設(shè)備點檢定修制是保持設(shè)備穩(wěn)定順行的有力保障。為深化點檢制,應(yīng)該建立健全了廠級、車間級和班組級三級點檢管理體系和網(wǎng)絡(luò),本著“簡單設(shè)備誰使用誰負(fù)責(zé)、復(fù)雜設(shè)備誰維修誰負(fù)責(zé)”原則,進(jìn)一步明確責(zé)任,加強考核,避免了只追求產(chǎn)量、不關(guān)心設(shè)備狀況、設(shè)備帶病運行現(xiàn)象的發(fā)生。
推行小時巡檢制和設(shè)備隱患故障分類控制體系,設(shè)備點檢應(yīng)該按照“定人、定點、定周期、定標(biāo)準(zhǔn)、定點檢計劃表、定記錄、定點檢工作流程和定點檢業(yè)務(wù)流程”的要求;制定崗位點巡檢制度,運用巡檢卡進(jìn)一步明確巡檢內(nèi)容、巡檢標(biāo)準(zhǔn)、巡檢時間和巡檢責(zé)任人,做到分工明確、協(xié)作密切、責(zé)任落實、作業(yè)標(biāo)準(zhǔn)化,使點巡檢切實起到預(yù)防預(yù)報的作用;為有效解決點巡檢過程中發(fā)現(xiàn)的各類問題,建立了設(shè)備隱患故障分類控制體系:一類故障利用定修時間排除,二類、三類故障通過巡檢和點檢即可控制,每天晨會車間依據(jù)“設(shè)備隱患故障分類控制整改表”提供的信息,安排當(dāng)日點檢重點,有效控制設(shè)備劣化趨勢,提高設(shè)備作業(yè)時間。
在點檢的基礎(chǔ)上,優(yōu)化定修模型。定修模型以點檢總結(jié)和分析為依據(jù),充分考慮各生產(chǎn)工序之間的聯(lián)系,盡最大可能減少物流和能源損失,以各生產(chǎn)工序間必要的物流平衡和能源平衡保證生產(chǎn)的平衡。為加強定修的動態(tài)管理和過程控制,應(yīng)建立定修前的準(zhǔn)備會制度,4小時以內(nèi)的定修提前2天召開會議、4小時以上的定修提前3天召開會議,落實方案、物資和工器具的準(zhǔn)備情況,明確定修內(nèi)容、責(zé)任和要求;定修中間適時召開中間會,落實解決定修中出現(xiàn)的新問題;確保定修都能做到內(nèi)容和措施及時、到位,定修完成后,及時組織人員對定修效果檢查驗收,召開定修反省會,寫出定修總結(jié)和寫實,再據(jù)此檢查點檢標(biāo)準(zhǔn)和定修模型,從而形成了PDCA良性循環(huán)。
全員參與設(shè)備點檢定修,實現(xiàn)了操檢合一。操作、維護(hù)和專業(yè)技術(shù)人員共同維護(hù)管理設(shè)備,操作者精心操作,維護(hù)者精心維護(hù)保養(yǎng),點檢定修信息互通有無,發(fā)現(xiàn)故障嚴(yán)格按分類控制,使設(shè)備運行始終處于動態(tài)受控狀態(tài)。
3、加強維護(hù)保養(yǎng)
設(shè)備的正常運轉(zhuǎn),首要是做好設(shè)備的維護(hù)保養(yǎng),誰主管,誰負(fù)責(zé)。“刀不磨要生銹”,維護(hù)保養(yǎng)更如此。每一個注油點每天需要加油100g,就必須每天加油100g,而決不允許在10天后一次性加油1000g,在潤滑保養(yǎng)上杜絕簡單的加法運算,嚴(yán)格按照“五定”、“三級過濾”原則進(jìn)行潤滑管理,為此崗位工必須真正負(fù)起責(zé)任。
自檢自修的內(nèi)容要切實可行,一絲不茍。崗位工發(fā)現(xiàn)問題后及時匯報,采取必要措施防患未然,同時交接班記錄必須詳實客觀,交接班時必須對設(shè)備進(jìn)行細(xì)致檢查,發(fā)現(xiàn)問題及時處理,杜絕帶病作業(yè)。
4、計劃檢修是頭等大事
設(shè)備的正常使用,操作、維護(hù)重要,檢修更重要。由于產(chǎn)量、質(zhì)量等因素,設(shè)備停機時間逐步減少,我們的檢修工恰似“110緊急警務(wù)”奮戰(zhàn)在搶修現(xiàn)場,油泥、汗水、塵土混在一起,確實感人,但是設(shè)備管理卻事倍功半。
為了改變被動局面,必須根據(jù)點檢情況、設(shè)備運行時間、設(shè)備負(fù)荷、設(shè)備所處環(huán)境、設(shè)備維修歷史記錄等因素科學(xué)地科學(xué)地制定計劃檢修計劃,設(shè)備技術(shù)員不定期的對所有設(shè)備進(jìn)行全面檢查,與機臺的檢修計劃匯總到車間,經(jīng)過認(rèn)真分析拿出解決方案,再將任務(wù)布置到檢修班組,根據(jù)生產(chǎn)情況實施檢修。檢修時設(shè)備技術(shù)人員親自到場,嚴(yán)格把關(guān),最后由設(shè)備技術(shù)人員與崗位工共同簽字驗收,實現(xiàn)互相監(jiān)督、相互制約,由三家共同對檢修質(zhì)量負(fù)責(zé),把事故消滅在萌芽狀態(tài),降低勞動強度與檢修成本,提高設(shè)備運轉(zhuǎn)率,保證生產(chǎn)。
5、建立難點攻關(guān)機制,解決制約生產(chǎn)的設(shè)備瓶頸問題。
針對制約生產(chǎn)和指標(biāo)提升的薄弱環(huán)節(jié),開展技術(shù)攻關(guān)揭榜、小改小革和合理化建議等活動形式,激發(fā)員工解決問題的積極性。把技術(shù)攻關(guān)的目標(biāo)鎖定在“三點”上,一是重點,二是難點,三是事故頻發(fā)點。通過建立和實施設(shè)備難點攻關(guān),有效地消除設(shè)備瓶頸,挖掘設(shè)備潛能。
6、建立教育培訓(xùn)機制,提高員工的業(yè)務(wù)技術(shù)素質(zhì)。
設(shè)備管理是企業(yè)的一項基礎(chǔ)管理,加強教育和培訓(xùn)、不斷提高各級設(shè)備管理人員的業(yè)務(wù)技能是提高設(shè)備管理水平和企業(yè)競爭力的重要手段。開展了各種形式的專業(yè)培訓(xùn)學(xué)習(xí)活動,組織員工學(xué)習(xí)了“5S”管理和各項管理制度,培養(yǎng)職工尊崇規(guī)則的習(xí)慣;組織工程技術(shù)人員對員工進(jìn)行技術(shù)技能培訓(xùn)學(xué)習(xí),從感性和理性上更好的認(rèn)知了設(shè)備,提升了素養(yǎng)水平;針對近年來新設(shè)備投產(chǎn)較多的特點,認(rèn)真組織員工培訓(xùn)學(xué)習(xí),使員工及時了解新設(shè)備的技術(shù)特性、掌握設(shè)備的運行特點。通過這些措施,使員工很快熟悉了新設(shè)備,為規(guī)范地使用設(shè)備奠定了基礎(chǔ)。
開展“相互性培訓(xùn)”活動,即利用每個人都有自己的強項特點,組成由技術(shù)員、區(qū)域維修負(fù)責(zé)人、生產(chǎn)班長為主的設(shè)備隱患大排查小組,對于各工序的重要控制點做逐一檢查,明確易發(fā)故障點、備品備件情況,并重新確定預(yù)檢修時間,一方面完善了預(yù)防性維修系統(tǒng),另一方面使每一位相關(guān)責(zé)任人對目前的設(shè)備狀況都有了更深層的了解等等。
7、充足備件是勝利之本
“巧婦難做無米之炊”。為了保證生產(chǎn)的正常運行,必須對備件進(jìn)行細(xì)致分類,總結(jié)出每一種易損件的使用周期,備件的經(jīng)濟訂購量,采購時間,和重定點,安全庫存量按實際使用的情況由系統(tǒng)不斷調(diào)整,使庫存?zhèn)浼?shù)量不斷趨于合理,減少備件費用。在合理控制庫存的前提下備足、備好備件,做到“手中有糧心不慌”。與此同時,與采購部門密切合作,堅持“貨比三家”的采購原則,并定期對供應(yīng)商進(jìn)行對比考察,共同保證備件質(zhì)量及供貨周期。同時對于那些關(guān)鍵和瓶頸設(shè)備的非易損件也要適當(dāng)儲備,以防不測,但要嚴(yán)格把握數(shù)量。
8、技改技措、修舊利廢
對于結(jié)構(gòu)簡單的易損件,自行或委外加工,即保證生產(chǎn),又節(jié)約資金。極力推行修舊利廢,分類處理更換下來的備件,堵住因備件使用導(dǎo)致的設(shè)備損壞停產(chǎn)的漏洞。對于確實有修理價值的零件進(jìn)行徹底修理,以備后用。鼓勵員工對設(shè)備中存在的不合理之處進(jìn)行技術(shù)革新與改造,改善設(shè)備的工作性能,也為員工創(chuàng)造學(xué)以致用的條件和機會。實現(xiàn)資源的重復(fù)利用,物盡其力,杜絕浪費,降低成本,減少污染。
9、設(shè)備管理服務(wù)于安全生產(chǎn)
生產(chǎn)以設(shè)備為基礎(chǔ),而安全則是生產(chǎn)與設(shè)備正常運轉(zhuǎn)的前提和保證,離開了安全就毫無價值。“安全第一,預(yù)防為主”,“我要安全,我會安全,我能安全”。設(shè)備的運轉(zhuǎn)處在一個動態(tài)之中,時刻都存在著不安全因素,所以必須時刻抓緊安全這一重要環(huán)節(jié),在平時的維護(hù)保養(yǎng)、計劃檢修、員工培訓(xùn)中無時不刻要提到安全,講到安全,考慮到安全,做好安全。當(dāng)設(shè)備與安全沖突時,設(shè)備必須服從安全,降低設(shè)備事故的發(fā)生機率,同樣是設(shè)備管理體制中的一個重要環(huán)節(jié)。
堅持預(yù)防性、系統(tǒng)性管理的原則,把查找隱患和消缺治理有機地結(jié)合起來,形成了定點、定時、定內(nèi)容的檢查制度。對設(shè)備隱患進(jìn)行全面排查,及時發(fā)現(xiàn)并對發(fā)現(xiàn)的不符合項深入剖析原因,制定具體的整改計劃和措施,進(jìn)行了全面整改。
10、抓好設(shè)備的現(xiàn)場管理。
企業(yè)要以“5S”管理為手段、促進(jìn)設(shè)備現(xiàn)場管理逐步向“客廳工廠”邁進(jìn)的目標(biāo)。通過廣泛的學(xué)習(xí)和宣傳,使廣大員工牢固樹立了“設(shè)備無故障始于無塵”的觀念,車間充分利用點檢和定修的時機抓好設(shè)備的清潔管理,現(xiàn)場的備件做到了分類定置管理;對蒸汽、供水、供氣等主管線進(jìn)行了整治,實現(xiàn)了主管線的“零泄漏”。
另外,設(shè)備基礎(chǔ)管理規(guī)范化的重點還包括各類設(shè)備臺帳的完善,技術(shù)圖紙電子化,整合維修、交接班等記錄,整理線路圖,建立單機臺設(shè)備檔案等。
欲速則不達(dá),企業(yè)在推行TPM設(shè)備管理的時候不可激進(jìn),要遵循其本身的原則,并結(jié)合自己的實際情況,不斷創(chuàng)新,找到一條適合本企業(yè)的發(fā)展道路。
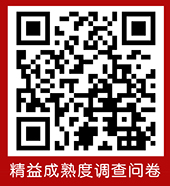